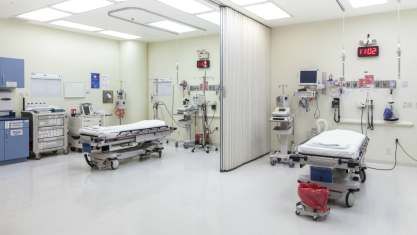
IOT solutions have great potential and allow you to increase productivity
Even before the pandemic, analysts at consulting firm McKinsey predicted that Industrial Internet of Things (IIoT – Industrial Internet of Things) by 2025globally will generate up to $3.7 trillion in value. While the global crisis has slowed their deployment in factories and warehouses, there is little doubt that the IIoT environment will continue to grow rapidly.
The Industrial Internet of Things will find its way into modern industry because it has great potential value and can help process massive amounts of data.
– The actual economic value of IIoT in the coming years may be a little less due to the coronavirus pandemic, but McKinsey’s forecast reflects the potential of these solutions to reduce downtime, increase productivity and efficiency and the level of utilization of enterprise resources – predicts Gerard Dermont, Regional Sales Director Poland and Baltics at Vertiv.
IIoT boundary calculation value
IIoT devices are m.in. Sensors, controllers or industrial computing platforms that provide greater insight into the operation and control of equipment that keeps businesses, warehouses and factories running. The hardware that enables industrial applications generates so much data in a short period of time that it is impossible to rely solely on the cloud for real-time analysis. This means that in many cases, reaping the benefits of the IIoT will require IT equipment to be installed in a warehouse or factory floor, where it is exposed to much more adverse environmental conditions than in a data center or office environment.
Infrastructure challenges associated with internet-connected industrial equipment
Enterprises planning to deploy edge infrastructure in industrial environments need to analyze in several areas listed below and consider how conditions observed in these environments may affect the performance of IT systems, putting them at risk.
Power variability– As with any location connected to the Internet, it is essential to implement backup power to prevent the occurrence of power outages. In production environments and automated warehouses, power conditioning can be even more important. Machines operating in these facilities often generate electrical noise that can interfere with IT equipment if power quality is not taken care of before it reaches the IT systems. Different types of UPS provide different models of power conditioning approaches, and the type of UPS chosen determines its effectiveness at removing disturbances. In harsh environments, an online double-conversion UPS is best, as it provides the cleanest alternating current.
Environmental conditions– In most industrial environments, it is impossible to maintain the temperature and humidity required for reliable IT equipment operation. Therefore, special cooling is required. In large, open areas of warehouses or factories, ventilation or air conditioning units are typically integrated into the IT equipment enclosure or mounted next to it.
Air quality– Industrial environments also have a higher concentration of airborne dust and particulates than, for example. in the data center. These contaminants can affect the reliability and lifespan of equipment if they are e.g. drawn in by server fans. Protecting equipment requires special, sealed cabinets or enclosures that prevent unfiltered air from entering the equipment. With cooling integrated into the enclosure, a clean, temperature-controlled environment is created, regardless of outside air quality.
Physical security– The basic premise of edge computing is to deploy servers and storage close to the people and devices they serve. In manufacturing, this usually means installing IT equipment in areas where there is a risk of unauthorized access by staff. Locking cabinets or alarm sensors on doors can help in this situation.
Coastal Infrastructure Visibility– Most remote, internet-connected locations are located in environments with limited technical resources. Remote monitoring software gives IT specialists an insight into the performance of the equipment, making sure it is working as intended. When equipped with additional sensors and remote monitoring tools, they can also generate alerts about situations that are potentially dangerous to the equipment, such as. elevated temperatures, flooding or unauthorized access.
– Companies deploying IIoT in harsh environments can do so by selecting the right power, chassis cooling and monitoring solutions that meet the requirements of the environment, and then integrating those components on-site – says Gerard Dermont. – However, this approach can increase deployment time, strain IT resources and make it difficult to standardize infrastructure across multiple sites. A better option is to use complete, integrated solutions, designed and tested to ensure the highest performance and reliability of IIoT devices – summarizes the Vertiv expert.